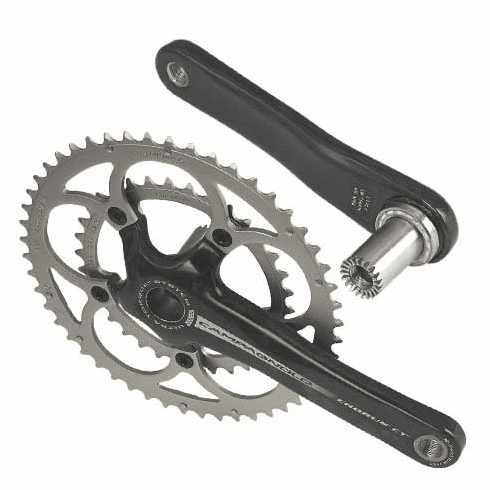

Campagnolo Chorus 2007 10 Speed Ultra-Torque Crankset, Campy Chorus
Campagnolo Chorus 2007 10 Speed Ultra-Torque Crankset, Campy Chorus
The 2007 Campagnolo Chorus� crankset with integrated bottom bracket has been completely redesigned with the new Ultra-Torque� technology.
The crank structure is always in unidirectional carbon combined with multidirectional carbon, to form a structure with great strength and rigidity. There is a low-density but uncompressible core inside it to resist the enormous pressures used in the special production process developed by Campagnolo� technicians.
The bottom bracket semi-axles are fixed directly to the carbon structure in which it was not therefore necessary to add another insert other than the one that houses the pedal thread.
The use of a large integrated axle and external cups has further improved the already considerably rigidity features. However this did not make it necessary to broaden the system laterally, especially in the bottom bracket zone, and allowed a weight reduction at the same time. As a result, riders can benefit from superior performance while maintaining the pedal cleat position unchanged on their soles and without suffering annoying interferences with the crank.
With its 2007 range Campagnolo� is introducing the new Ultra-Torque� crankset with integrated bottom bracket. This is the effective response to the demand for a new system finally superior in every detail to the traditional, reliable and well-tried ISO spindle.
Only a system which would be truly innovative and significantly improved, compared with any alternative available on the market, could convince Campagnolo� to abandon a product which can boast of decades of performance at the highest level.
The Ultra-Torque� system has been developed by the Campagnolo� R&D team which has always worked in symbiosis with the racing world and enthusiasts, with a double aim: design a superior product and put an end to the weaknesses of the existing system.
In fact, for example, if on the one hand external cups were appreciated because of the slight increase in the system's rigidity, on the other hand the increase in the lateral dimensions of the cranks in the ankle/heel area was a nuisance and made it necessary to broaden the pedal stroke.
Furthermore, there was a great need to create a more immediate, secure and simpler crank fixing system which would not require continuous monitoring, combined with the aim of rendering the disassembly, reassembly and maintenance operations easier and fast.
The front coupling of the Hirth type is self-aligning and self-centring, but it has to be preloaded if it is to work properly and transform the two semi-axles into a solid and very rigid shaft: this function is provided by the spring washer of the central fixing screw which exerts a pressure of 600kg/1300lb on the coupling.
In this way, the oversize axle of the Ultra-Torque� bottom bracket behaves for all intents and purposes as if it were made in a single, extremely strong and ultra-rigid piece.
Each semi-axle is therefore joined integrally to the crank, fixed by interference in the case of aluminium cranks and by special bonding in the case of carbon cranks; the bearings are driven by interference onto the semi-axles while the seals that protect the bearings are mounted both on the semi-axles and on the cups.
What are the advantages of this new generation of Ultra-Torque� cranksets with integrated bottom bracket?
Lightness Thanks to the lightness of the oversize axle and, in the case of carbon ones, because the cranks no longer have metal inserts on which to fix the bottom bracket axle, but incorporate the axle itself directly.
Rigidity Thanks to the external caps and greater diameter of the oversize axle.
Ergonomics The greatest advantage, however, derives from the fact that there is more space left for the ankles and shoes of the athlete who will not be obliged to shift the cleats to broaden the position of the feet and therefore of the pedal stroke. The Q factor also remains unchanged from the already excellent values previously offered by Campagnolo�.
By increasing the diameter of the bottom bracket axle in the interface zone with the crank it was possible to reduce the thickness of the cranks, moving the bearings outside the bottom bracket without increasing the lateral dimensions of the crankset.
Then, a technical solution designed for aircraft engine shafts was adopted in order to make it possible to insert the bearings: a bottom bracket axle composed of two semi-axles joined integrally with a joint of the Hirth type. In fact, by splitting the axle into two halves, the bearings are inserted from the centre, and it is therefore possible to increase the diameter of the interface area between the semi-axle and crank just enough to reduce the thickness of the same and thereby increase the lateral space available for the pedal stroke.
It is worthwhile to underline, in a bottom bracket with external cups, that the flexion is maximum between the bearing and crank and minimum between the mid-point of the axle where there is mostly a transmission of torque
Maintenance/Functionality
Standard wrenches are used to tighten the light allow caps, while a normal 10mm socket wrench is used for the central screw that unites the axle.
The tightness of the screw is very intuitive because you "sense" the compression of the spring and clearly feel it when compression is complete because of the exponential increase of the resistance. Another function of the spring, which is mounted on the screw and cannot be removed, is to prevent unscrewing.
Finally, extremely high-precision and oversize bearings complete the system. They offer great smoothness and very low friction, are protected, as we have said, by two seals and are very easy to change.
So it appears clear that the Ultra-Torque� system is a fundamental evolutionary step, which hits the bull's-eye of the target Campagnolo� set itself: a new system which improves the existing ones from every point of view.
Ultra Torque Overboard Cups required and sold separately
The 2007 Campagnolo Chorus� crankset with integrated bottom bracket has been completely redesigned with the new Ultra-Torque� technology.
The crank structure is always in unidirectional carbon combined with multidirectional carbon, to form a structure with great strength and rigidity. There is a low-density but uncompressible core inside it to resist the enormous pressures used in the special production process developed by Campagnolo� technicians.
The bottom bracket semi-axles are fixed directly to the carbon structure in which it was not therefore necessary to add another insert other than the one that houses the pedal thread.
The use of a large integrated axle and external cups has further improved the already considerably rigidity features. However this did not make it necessary to broaden the system laterally, especially in the bottom bracket zone, and allowed a weight reduction at the same time. As a result, riders can benefit from superior performance while maintaining the pedal cleat position unchanged on their soles and without suffering annoying interferences with the crank.
With its 2007 range Campagnolo� is introducing the new Ultra-Torque� crankset with integrated bottom bracket. This is the effective response to the demand for a new system finally superior in every detail to the traditional, reliable and well-tried ISO spindle.
Only a system which would be truly innovative and significantly improved, compared with any alternative available on the market, could convince Campagnolo� to abandon a product which can boast of decades of performance at the highest level.
The Ultra-Torque� system has been developed by the Campagnolo� R&D team which has always worked in symbiosis with the racing world and enthusiasts, with a double aim: design a superior product and put an end to the weaknesses of the existing system.
In fact, for example, if on the one hand external cups were appreciated because of the slight increase in the system's rigidity, on the other hand the increase in the lateral dimensions of the cranks in the ankle/heel area was a nuisance and made it necessary to broaden the pedal stroke.
Furthermore, there was a great need to create a more immediate, secure and simpler crank fixing system which would not require continuous monitoring, combined with the aim of rendering the disassembly, reassembly and maintenance operations easier and fast.
The front coupling of the Hirth type is self-aligning and self-centring, but it has to be preloaded if it is to work properly and transform the two semi-axles into a solid and very rigid shaft: this function is provided by the spring washer of the central fixing screw which exerts a pressure of 600kg/1300lb on the coupling.
In this way, the oversize axle of the Ultra-Torque� bottom bracket behaves for all intents and purposes as if it were made in a single, extremely strong and ultra-rigid piece.
Each semi-axle is therefore joined integrally to the crank, fixed by interference in the case of aluminium cranks and by special bonding in the case of carbon cranks; the bearings are driven by interference onto the semi-axles while the seals that protect the bearings are mounted both on the semi-axles and on the cups.
What are the advantages of this new generation of Ultra-Torque� cranksets with integrated bottom bracket?
Lightness Thanks to the lightness of the oversize axle and, in the case of carbon ones, because the cranks no longer have metal inserts on which to fix the bottom bracket axle, but incorporate the axle itself directly.
Rigidity Thanks to the external caps and greater diameter of the oversize axle.
Ergonomics The greatest advantage, however, derives from the fact that there is more space left for the ankles and shoes of the athlete who will not be obliged to shift the cleats to broaden the position of the feet and therefore of the pedal stroke. The Q factor also remains unchanged from the already excellent values previously offered by Campagnolo�.
By increasing the diameter of the bottom bracket axle in the interface zone with the crank it was possible to reduce the thickness of the cranks, moving the bearings outside the bottom bracket without increasing the lateral dimensions of the crankset.
Then, a technical solution designed for aircraft engine shafts was adopted in order to make it possible to insert the bearings: a bottom bracket axle composed of two semi-axles joined integrally with a joint of the Hirth type. In fact, by splitting the axle into two halves, the bearings are inserted from the centre, and it is therefore possible to increase the diameter of the interface area between the semi-axle and crank just enough to reduce the thickness of the same and thereby increase the lateral space available for the pedal stroke.
It is worthwhile to underline, in a bottom bracket with external cups, that the flexion is maximum between the bearing and crank and minimum between the mid-point of the axle where there is mostly a transmission of torque
Maintenance/Functionality
Standard wrenches are used to tighten the light allow caps, while a normal 10mm socket wrench is used for the central screw that unites the axle.
The tightness of the screw is very intuitive because you "sense" the compression of the spring and clearly feel it when compression is complete because of the exponential increase of the resistance. Another function of the spring, which is mounted on the screw and cannot be removed, is to prevent unscrewing.
Finally, extremely high-precision and oversize bearings complete the system. They offer great smoothness and very low friction, are protected, as we have said, by two seals and are very easy to change.
So it appears clear that the Ultra-Torque� system is a fundamental evolutionary step, which hits the bull's-eye of the target Campagnolo� set itself: a new system which improves the existing ones from every point of view.
Ultra Torque Overboard Cups required and sold separately